Top 10 Factors to Consider While Choosing the Better End mill Grinder
2023-07-20Machinery From:Lets Media
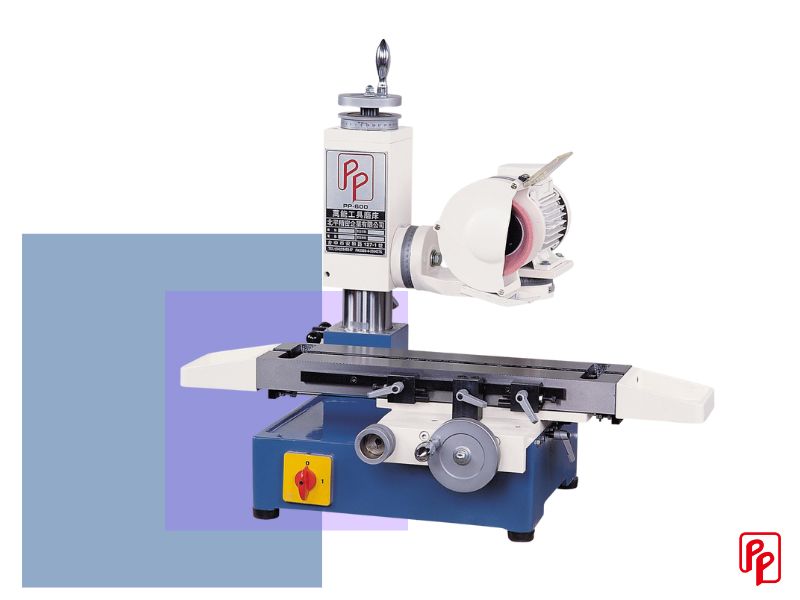
Top 10 Factors to Consider While Choosing the Better End mill Grinder
If you have ever been working with metal, you're likely made aware of the need for an endmill grinder.
The type of endmill you want for your grinder depends on your application. There are multiple factors to consider when selecting an endmill for your milling and grinding needs, such as cutting speed, size, diameter, rake, and crown style.
Of course, endmills come in many types, shapes, and sizes, depending on your application. We have created a grinder selection guide to help you make the best application choice. The purpose here is to explain which endmill grinder you should choose and why.
Top 10 Factors to Consider While Choosing the Better Endmill Grinder
1. Key Characteristics of an End Mill
Many factors affect the performance of an end mill. A good choice will have a shank and cutter diameter that are both appropriate for your application, as well as appropriate levels of wear resistance.
The number of flutes is also important because it determines how many times you can use a single tool in one direction before changing directions.
You must also consider what material you'll be grinding with your end mill—will it be steel or aluminum?
2. Shank & Cutter Diameter
The shank diameter is the internal diameter of your end mill, which is where it gets inserted into the workpiece. The cutter diameter is the thickness of your bit or tool that you're using to cut material.
It's important to keep these two measurements in mind when selecting an end mill because they can vary greatly. It depends on the material you're working with and how much force will be required to break through it.
For example
If you want an aggressive cut without resistance from your material, choose a smaller shank size so there's less resistance when pressing down on materials.
3. How Many Flutes Should I Choose?
The number of flutes is the number of cutting edges, which should equal or be greater than the number of cutting edges in your tool. The rule for selecting endmills is to use at least four flutes for a 3-flute tool and six for an 8 -flute.
The best way to determine if you need more than one flute is by looking at how quickly your material will cut through with each type of cutter.
Try them all if you're unsure which cutter will work best with your material! That way, if something doesn't seem right, try again until they work well together.
4. Number of Abrasives
The number of abrasives in an end mill is between three and five.
The most common types are:
- Ceramic or silicon carbide: silicon carbide is more brittle, so it's used for cutting harder materials such as steel or aluminum)
- Aluminum oxide (alumina) is less brittle than silicon carbide but still has some strength in the end mill. It's used for cutting softer materials like plastics and rubber.
5. Size of the Grinding Wheel
The size of the grinding wheel is important. The diameter of your endmill is measured in inches ("I") and millimeters (mm). You can adjust these measurements accordingly if you want a wider or narrower workpiece.
#For example
If you wanted to cut something with a 0.5 mm diameter hole in it, then this would be done by using an endmill with a 1-inch diameter and a 50 mm long pointy tip at its front end.
Suppose multiple heads on an axis spindle can move back and forth on their axes at different speeds along its length. Then their combined diameters should also be considered when selecting an appropriate size for your project needs.
6. What Material Should You Choose For Your End Mill?
The type of material being cut is also important—what does this particular application call for? The size and shape of your workpiece may also dictate how much flexibility your endmills need.
#For example
If you are cutting steel on a Jacobs Bench Mounting System (JBM), using an 8 mm diameter × 1/2" long End Mill with a straight flute pattern won't be any flexibility.
However, if this same tool were used on another machine, such as a CNC Mill or Lathe, there would be movement between each tooth due to its size and shape.
7. Should Your Helix Angle Be Higher Or Lower?
You might wonder, "Should my helix angle be higher or lower?" Well, that depends on what you plan to do with your endmill. If you want a very aggressive cut and will be doing lots of cuts with different tools, then it is better to have the helix angle at a higher value.
On the other hand, if you only need to make a few cuts per tool and don't want an aggressive cut. Then it would be better to keep the angle lower so that fewer changes are required for each tool change.
8. Magnetic Chuck
A magnetic chuck is a very effective way to hold the endmill. It's safer, more accurate, and more expensive than a collet chuck. The downside is that it's not as easy to use for milling small parts.
A collet chuck can be used with any spindle. Still, it's only available on some machines with an internal spindle and hand wheel drive that uses a tool post or pinion gear to drive the spindle employing a lever mechanism inside the machine housing.
When using this system, you'll need additional adapters if you want to mount your machine onto another lathe or milling machine. These usually come in sets containing several sizes depending on the attachment method best suits your needs.
9. Adjustable Speed
Adjustable speed is a must-have feature for any grinding machine. It enables you to regulate the speed of your machine and boost output. The best endmills have an adjustable speed dial that ranges from 0 to 3200 rpm and has been calibrated for different applications, as metalworking or fabricating dies.
10. Adjustable Feed Rate
You can change the speed of the milling machine thanks to the adjustable feed rate, which is a terrific feature. It can change the milling machine's and cutting tool's speed.
Conclusion
We hope that this guide has been helpful for you in finding the best grinder for your next project. We've compiled a list of 10 factors to help you hone your selection criteria and ultimately gain the best choice by relying on reviews from users who have used these tools.
Pei Ping is one of the best places to buy Endmill Grinder from. We have a comprehensive choice of goods to meet your grinding and machine needs. Moreover, we are a professional manufacturer, supplier, and exporter of Endmill grinders.
Therefore, Pei Ping is the only firm you need to consider if you're looking for a dependable supplier of the highest quality and service. We aim to provide high-quality products and good service for our customers. We hope you will enjoy shopping at Pei Ping.