Maintenance and Operational Best Practices for Water Jet Cutting Systems
2024-05-02Mould & Die
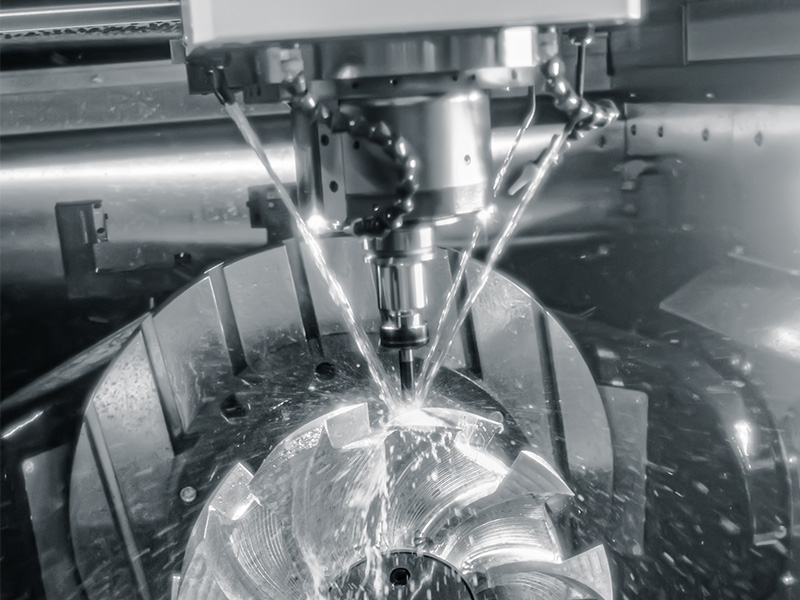
Introduction
At Golden Automatic Co. Ltd., we pride ourselves on leading the way in industrial excellence. One of the most versatile tools in our arsenal is the water jet cutting system, a pinnacle of precision and efficiency. However, like any sophisticated machinery, its performance heavily relies on proper maintenance and operation. In this article, we delve into the best practices that ensure your water jet cutting system operates at peak performance.
Understanding Water Jet Cutting Systems
Water jet cutting employs a high-pressure stream of water, sometimes mixed with abrasives, to cut through a variety of materials. It's favored for its precision and ability to cut without introducing heat or stress to the material. Key components include the high-pressure pump, cutting nozzles, and an abrasive feed system, each playing a critical role in the cutting process.
Key Components of Water Jet Cutting Systems
Water jet cutting employs a high-pressure stream of water, sometimes mixed with abrasives, to cut through a variety of materials. It's favored for its precision and ability to cut without introducing heat or stress to the material. Here's a closer look at its key components:
- High-Pressure Pump: The heart of the water jet system, the high-pressure pump, pressurizes water to extremely high levels — often up to 60,000 psi or more. This high pressure is essential for enabling the water stream to cut through hard materials. The efficiency and reliability of the pump directly influence the cutting performance and speed.
- Cutting Nozzles: These are precision-engineered components where the high-pressure water, often mixed with abrasive particles, exits to form a coherent jet stream. The nozzle's design and condition significantly affect the accuracy and quality of the cut. A well-maintained nozzle ensures a straight, clean cut, while a worn nozzle can lead to reduced precision and efficiency.
- Abrasive Feed System: When cutting harder materials like metal or stone, an abrasive, typically garnet, is added to the water stream. The abrasive feed system controls the rate at which this abrasive is mixed with the high-pressure water. This system is crucial for maintaining the consistency of the abrasive flow, which in turn influences the cutting power and finish of the cut.
Each of these components plays a vital role in the overall operation of a water jet cutting system. Regular maintenance and understanding of these parts are crucial for ensuring optimal performance and extending the life of the equipment.
Pre-Operational Checks
Before commencing any cutting task, a thorough inspection of the system is crucial. This includes checking for leaks in hoses, ensuring nozzles are not blocked, and verifying the integrity of the pump and control systems. Safety is paramount; always ensure that all safety guards are in place and that operators are wearing appropriate protective gear.
Operational Best Practices
Optimal operation of a water jet cutter involves more than just loading material and starting a cut. Adjusting cutting speeds, managing pressure, and controlling the abrasive flow rate are essential for achieving clean cuts and reducing wear on the system. Each material, whether it be metal, glass, or composite, requires specific settings for best results.
Maintenance Protocols
Routine maintenance is the key to longevity and consistent performance. Daily checks should include inspecting hoses and nozzles for wear. Weekly, the focus should shift to filters and seals, while monthly maintenance should involve a thorough check of the pump and electrical systems. Addressing issues promptly prevents more significant problems down the line.
Enhancing Longevity and Performance
Upgrading your water jet system with the latest technology can significantly boost its performance. Using high-quality abrasives and replacement parts extends the life of the system. Regular professional servicing ensures that your equipment is always running optimally.
Training and Skill Development
The skill of the operator is just as important as the quality of the machine. Regular training sessions help operators stay abreast of the latest techniques and safety standards. At Golden Automatic Co. Ltd., we emphasize the importance of continuous learning and adherence to best practices.
Environmental and Safety Considerations
While water jet cutting is more environmentally friendly than many alternatives, proper disposal of used water and abrasives is essential. Ensuring a safe working environment is not only a regulatory requirement but a moral obligation to every staff member.
Conclusion
In mastering the maintenance and operation of water jet cutting systems, attention to detail and a commitment to best practices are non-negotiable. The high-pressure pump, cutting nozzles, and the abrasive feed system are more than just parts of a machine; they are the keystones to unlocking efficiency, precision, and longevity in your cutting operations.
At Golden Automatic Co. Ltd., our dedication to providing top-tier solutions extends beyond the sale of equipment. We invite you to engage with us — whether it's for advanced training, consultation on upgrading your systems, or routine maintenance services. By partnering with us, you ensure that your operations remain not just efficient and productive, but also at the cutting edge of industry standards.
Remember, the performance of your water jet cutting system directly reflects the care and expertise invested in it. We encourage you to take these best practices to heart, prioritize regular maintenance, and continuously seek improvements in your operational techniques. Let's work together to achieve the pinnacle of precision and efficiency in water jet cutting.