Essential Components of Plastic Injection Molding: FengZhou's Insight into Their Critical Roles
2024-05-02Mould & Die
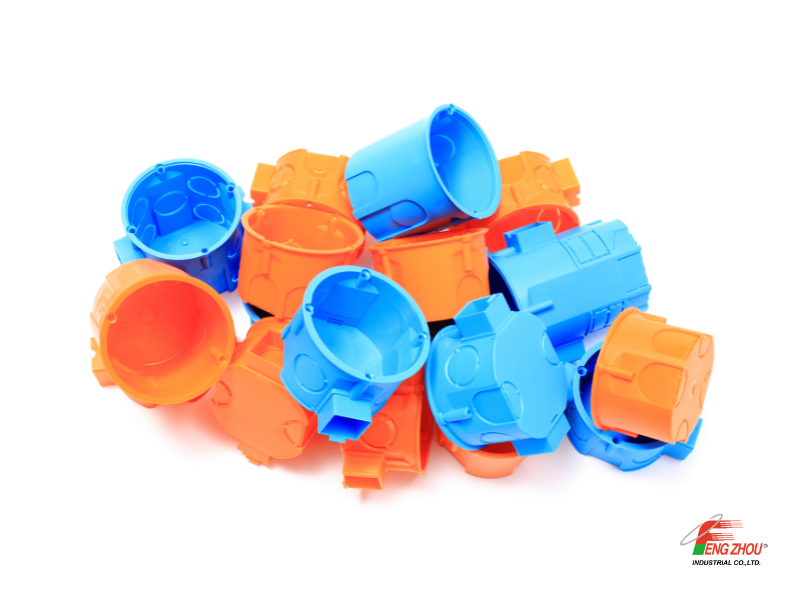
Introduction
In the sophisticated world of plastic injection molding, the quality of every part hinges on the precision and reliability of its mold components. FengZhou stands at the forefront of this technology, crafting essential components that ensure the efficiency of production and the excellence of the final product. From guide pins that ensure flawless alignment to support pillars that provide unwavering stability, join us as we delve into these components and their indispensable roles in injection molding.
Core and Cavity: The Blueprint of Precision
Central to FengZhou's mold-making prowess are the core and cavity, the yin and yang that define the internal and external contours of every molded part. Our dedication to precision ensures that these critical components consistently produce parts that meet our clients' exact specifications.
Guide Pins and Bushings: Alignment Maestros
Alignment is non-negotiable in injection molding, and FengZhou's guide pins and bushings are designed to meet this challenge. These components guarantee that mold halves come together with perfect precision, eliminating defects and enhancing the mold's longevity.
Return Pins: The Reset Rhythm
Each injection cycle's success is reset by FengZhou's return pins, ensuring the ejector system is primed for the next cycle. This rhythm is vital for maintaining consistent production speeds and quality.
Puller Bolts: Bonds of Strength
Puller bolts play a specialized and crucial role in the plastic injection molding process, particularly in the context of mold maintenance, assembly, and disassembly. These components are designed to facilitate the removal of molds or mold components from the injection molding machine or to assist in the ejection of parts from complex molds. Their unique design and application ensure the smooth operation of the molding process, contributing to maintenance efficiency and reducing downtime.
Support Pillars: The Foundation of Stability
FengZhou's support pillars are the bedrock of even pressure distribution throughout the molding process. This foundation prevents mold deformation, ensuring each part is a testament to durability and precision.
Sprue, Runner, and Gate: Pathways of Perfection
- The Sprue: Serving as the initial channel, the sprue directs molten plastic from the injection nozzle into the mold. Its design is crucial for minimizing pressure loss and ensuring a smooth flow of plastic.
- The Runner: From the sprue, the molten plastic flows into runners, which are channels cut into the mold plates. Runners distribute the plastic to one or several gates, and their layout is meticulously planned to ensure even filling of all cavities with minimal waste and cooling time.
- The Gate: The gate is the final narrow channel that directs the plastic into the mold cavity itself. The gate's size and type can significantly affect the appearance, structural integrity, and dimensional accuracy of the finished product. Proper gate design ensures minimal stress, reduced blemishes, and easy removal of the part from the mold.
Vents: Breath of Quality
Vents are precisely engineered gaps or channels within the mold that allow air and gases to escape from the mold cavity during the injection of molten plastic. These gases are produced from the heated plastic and the air initially trapped within the mold cavity. Without a proper escape route, the trapped air can cause a variety of defects in the final product, such as incomplete filling, burn marks, or surface blemishes.
Cooling and Heating Systems: Temperature Guardians
Cooling and heating systems are integral to the plastic injection molding process, providing the necessary temperature control to ensure high-quality production. While these systems are not part of FengZhou's product lineup, their importance cannot be understated in achieving the optimal thermal conditions for molding operations.
- Cooling systems typically consist of water or coolant channels running through the mold, absorbing heat from the molten plastic and the mold itself. The design of these channels is crucial for achieving uniform cooling, preventing warping or distortion of the part.
- Heating systems, on the other hand, may use electrical heaters or hot oil circulating through channels to maintain the mold at the required temperature. These systems are particularly important for molding materials with high melting points or for creating parts with intricate geometries.
Sliders and Lifters: Architects of Complexity
- Sliders, or side-actions, are movable components within the mold that slide into the cavity to form undercuts or side features on the part. These features are not aligned with the mold's opening and closing direction, necessitating a lateral movement mechanism. Sliders are activated by the mold's opening motion, typically through angled pins or hydraulic cylinders, allowing for the creation of complex shapes without compromising the mold's or part's integrity.
- Lifters, similar to sliders, are used to create angled undercuts or recesses that are not parallel to the mold's opening direction. They operate on a principle similar to sliders but are generally used for smaller or more intricate undercuts. Lifters lift or tilt a portion of the mold cavity or core to allow for the ejection of parts with complex geometries. Like sliders, they are often activated by the movement of the mold, utilizing cams or wedges to achieve the necessary movement.
Conclusion
FengZhou's commitment to excellence is reflected in each mold component we produce, from guide pins that ensure precise alignment to cooling systems that perfect the molding process. Our expertise not only powers the injection molding industry but also pushes the boundaries of what can be achieved, ensuring that every product made using our components is a testament to the highest standards of quality and efficiency.
By prioritizing precision, reliability, and innovation in every component, FengZhou continues to empower the manufacturing sector, enabling the creation of superior plastic parts that are integral to a myriad of applications across industries. This exploration of injection molding components is not just an educational journey but a celebration of FengZhou's role in shaping the future of manufacturing.